Implementation of Private GPTs in supply chain management
Integrating a Private GPT-based Generative AI assistant into supply chain management to process information in real-time, and seamlessly navigate through logistics, demand forecasting, inventory management, freight forwarding, and finance functions
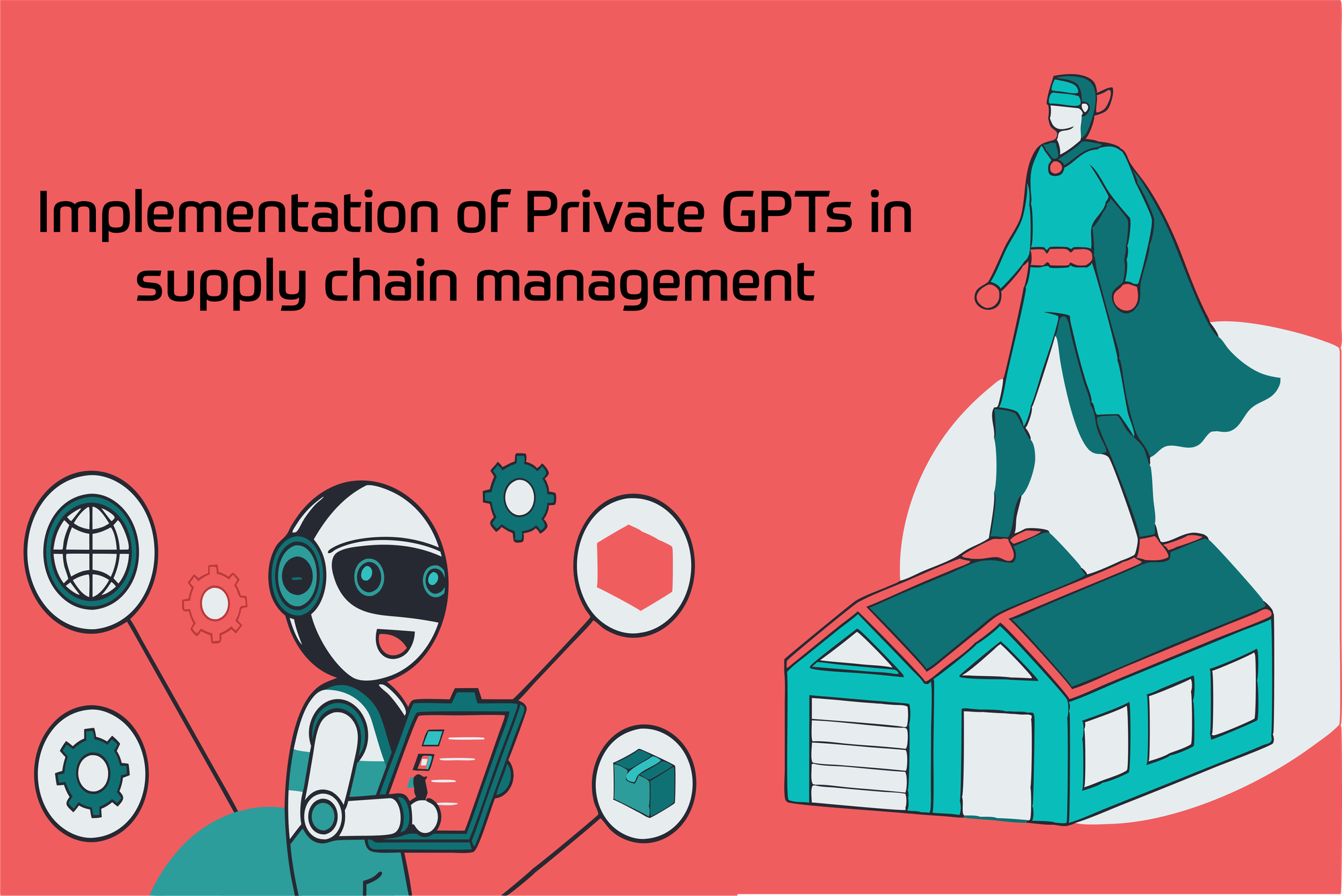
“The merit of any piece of software ties into how obvious its implementation seems to business leaders when they are pitched the idea”
This quote comes from a treasured client of Codemonk, sharing their feedback on a recently implemented piece of GenAI based solution. To add some context to this quote, let me walk you through the collaborative effort. The client in question approached Codemonk to optimise their supply chain operations to gain more control over tickets/queries raised by customers. This supply chain leader noticed their Google ratings taking a nose dive due to unresolved customer complaints concerning delayed shipments. Due to unforeseen circumstances, our client had little control over shipments already in transit. They faced issues such as
- Damaged shipping labels, which resulted in shipments getting stuck at distribution hubs
- Improper communication between logistics centres that led to customers not receiving timely updates for their shipment
- Lack of an efficient tracking mechanism, despite the implementation of GPS-based trackers and last-mile delivery solutions
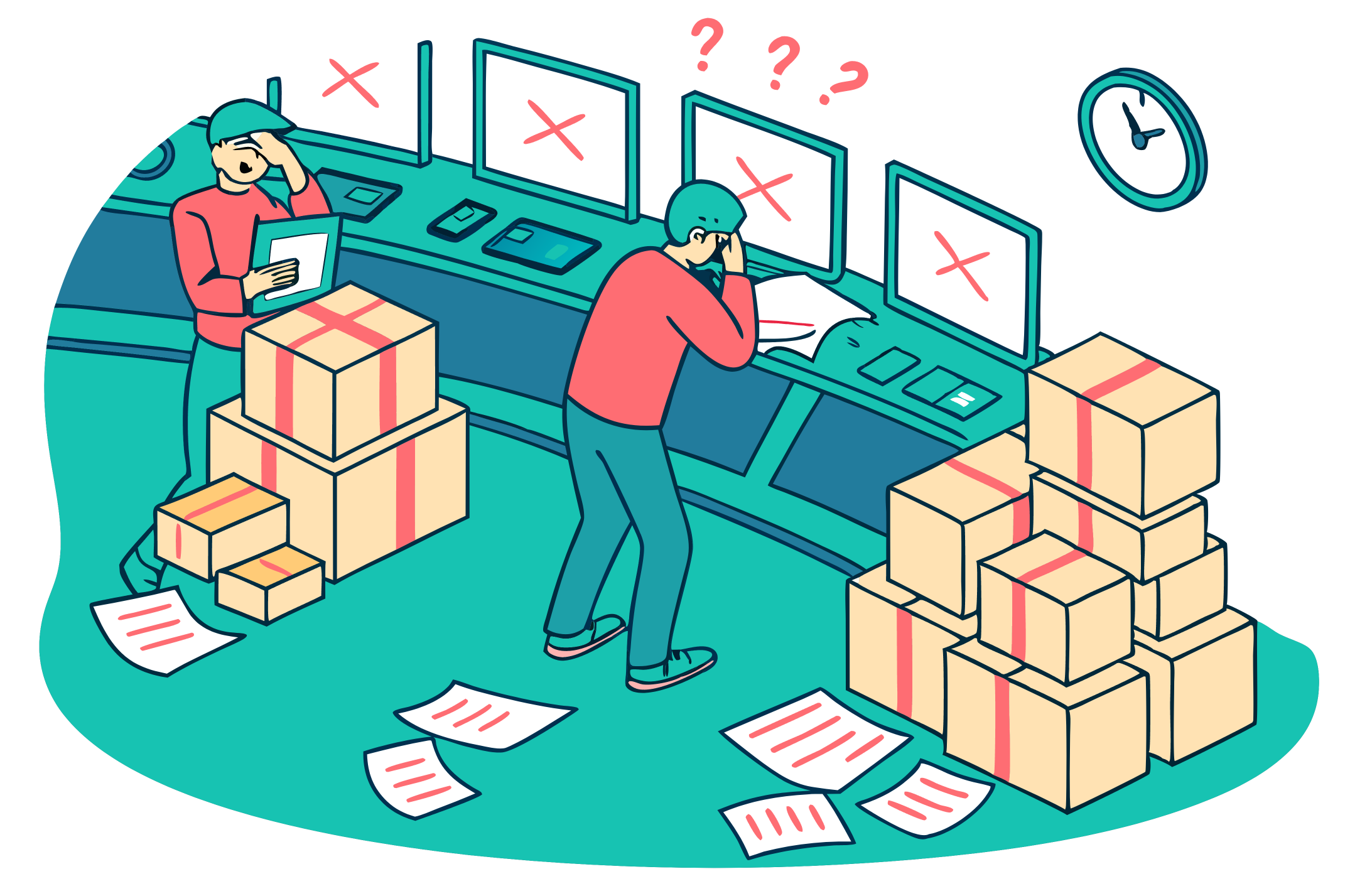
Although our initial sit down with the client uncovered several bottlenecks in software connecting the different hardware components, the more glaring issue was the customer service executives being unable to receive timely information about shipments in transit from forwarding partners, due to which they could not address issues arising from customers. Even though the account managers were experts at customer retention, they could not understand the nuances of freight forwarding as a business function, and as a result, lost the trust customers had placed in the brand.
Realising these issues first hand, the supply chain leader had looked at multiple robotics process automation (RPA) solutions that did not yield satisfactory results, which is when they reached out to Codemonk for a more intelligent solution.
Their requirement was crystal clear, “We do not care about how the technology works, but rather, it should simply work as intended, EVERY TIME.”
Codemonk’s approach to resolving this multifaceted problem was simple.
- Solving shipment label tampering - Using NPL & OCR to recreate damaged QR codes, Codemonk ensured that every label scanned provided all necessary information to freight forwarders (or virtually recreated when damaged), such that no delay occurred due to wear and tear of shipping labels
- API Integration Across Departments: Team Codemonk designed an ML solution that could access all relevant data through APIs connecting logistics, planning, forecasting, inventory systems, financial records, and customer databases, guaranteeing a 360-degree view of the business at any instance in time
- Data Centralization and Governance: Next, building central data lake ensured that every piece of information flowing across the business is accurate, up-to-date, and secure. With well-defined data governance protocols, the supply chain business could operate within regulatory and company-specific guidelines.
- Natural Language Processing (NLP): Incorporating a sophisticated NLP layer, along with a GenAI-driven chatbot, enabled account managers to understand complex supply chain queries and provide actionable insights in plain, simple language.
- Customizable Knowledge Base: Industry-specific terminology and business nuances were then programmed into GenAI chatbot & the ML model, making the combination a highly specialized supply chain assistant.
- Security and Privacy: End-to-end encryption, role-based access controls, and strict adherence to data privacy laws ensured sensitive information is always protected.
At the end of this development pipeline, Codemonk had designed a Private GPT tailored to the supply chain business, which more or less functioned as a new member within supply chain management team—an expert who never sleeps, processes information in real-time, and seamlessly navigates through logistics, demand forecasting, inventory management, freight forwarding, and finance functions. This was the transformative promise of implementing an ML-powered Generative AI assistant.
Next challenge at hand was Introducing the AI assistant the way one would introduce a new employee joining the organisation, ensuring that the process carried a human touch and not feel technologically heavy for the users.
- Phase 1: Needs Assessment: We recognised key pain points, such as inventory delays or manual data reconciliation, such that the GenAI chatbot could provide right information at the right time and upon specific requests or triggers made by the customer-facing function of the supply chain business.
- Phase 2: System Integration: Connecting the GenAI chatbot to all relevant systems and running an initial data ingestion pipeline, Team Codemonk simulated multiple real-world use cases to understand bottlenecks faced by the business.
- Phase 3: Training and Calibration Next, we fine-tuned the ML model with historical data and test scenarios to ensure it delivered accurate and relevant insights, all the while familiarising users with all such scenarios and the ideal pathway to resolving queries/tickets.
- Phase 4: User Training and Feedback Loop: Ultimately, we conducted train exercises with employees, allowing them to interact with the GenAI chatbot and establish feedback loops for continuous improvement.
A governing committee comprising IT, compliance, and business unit leaders was established to oversee the AI-driven operations. Regular audits and system updates would ensure the ML-model evolves with the business.
Upon implementation and running test cases, we documented the below results in 3 months
1. Enhanced Productivity
The ML model instantly retrieved critical information, such as real-time inventory levels or delivery timelines. This reduced the time spent searching for data across multiple systems by 80 percent, enabling employees to focus on strategic decision-making.
2. Reduced Downtime
By monitoring systems in real-time, Codemonk’s deployed ML model could predict potential disruptions, such as delays in freight and suggest proactive measures. This ensured smoother operations and fewer interruptions, restricting the total downtime to just a 20 minutes across 3 months.
3. Elimination of Redundancies
Team Codemonk was successful in automating routine tasks, such as generating invoices or reconciling accounts, eliminating manual errors and duplicate efforts. Tampering of shipment labels and QR codes was never a concern after deployment, as any wear and tear was immediately corrected for using OCR technology by virtually recreating damaged labels.
4. Revenue Growth and Cost Reduction
With better demand forecasting and optimized inventory management, the supply chain business documented a reduction in wastages by 70 percent. Real-time insights into freight and distribution channels minimized transportation costs while maximizing delivery efficiency.
Supply chain assisted by Private GPT
1) Consider this scenario: A logistics manager receives an inquiry from a client about the status of their shipment. Instead of sifting through spreadsheets and emails, the manager asks the AI: “Where is shipment #34567?” Within seconds, the AI replies with detailed information, including the shipment’s current location, estimated time of arrival, and any potential delays.
Meanwhile, the finance team queries the AI for outstanding invoices related to the shipment, and the AI promptly provides the necessary details. The inventory manager checks stock levels and replenishment schedules, all through a simple chat interface.
This seamless flow of information transforms how departments collaborate, driving efficiency and customer satisfaction.
2) Now, imagine a customer raising a ticket regarding a consignment lost in transit at the airport. And, the supply chain company has provided shipment insurance to cover potential losses. Here’s how Private GPT swiftly resolves the issue:
1. Immediate Ticket Acknowledgment and Data Retrieval
Upon receiving the ticket, the chatbot immediately acknowledges the customer’s concern and retrieves all relevant shipment data from connected systems:
- The shipment’s origin and destination
- The tracking history and last known location
- The insurance policy details and coverage limits
2. Real-Time Coordination with Stakeholders
The GenAI chatbot notifies key stakeholders, including the buyer, seller, and insurance team. It generates an automated report detailing the shipment’s status and potential next steps.
3. Root Cause Analysis and Solution Recommendation
Using historical data and predictive analytics, the chatbot identifies the most likely cause of the loss—e.g., mislabeling or customs clearance issues. It suggests actionable steps, such as filing a claim with the airport’s logistics team or requesting a replacement shipment from the seller.
4. Streamlined Insurance Claim Processing
The GenAI chatbot assists the customer in filing an insurance claim by:
- Pre-filling claim forms with relevant shipment details
- Attaching necessary documentation, such as invoices and tracking logs
- Providing real-time updates on the claim’s progress
5. Continuous Communication and Support
Throughout the resolution process, the AI keeps all parties informed via regular updates. The buyer receives assurance that their losses are covered, while the seller and logistics teams gain insights into preventing similar incidents in the future.
Conclusion: When rather than Why?
A key take away from this collaboration was the fact that, integrating a Private GPT-based Generative AI assistant into supply chain management is not just a technological upgrade—it’s a strategic imperative. By bridging gaps between departments and providing real-time, actionable insights, this GenAI solution becomes an indispensable member of the team. It empowers businesses to operate with greater agility, precision, and foresight, ultimately boosting both the top and bottom lines.
In retrospect, for supply chain companies ready to embrace the future, the question isn’t, “Why implement a Private GPT?”, but rather, “How soon can they get started?”
Reach out to us for a strategic overhaul of your business.